Paul,
In evaluating a FCAW weld cross section to AWS D1.1:2010, the weld engineer has asked that the CJP groove weld be evaluated by 4.9.4.1 for PJP. This is a requirement that the weld engineer has asked for.The Macro weld cross section as evaluated, revealed anomalies in the base material (A36), see photo. In the cross section the base material shows laminations. Under higher magnification the laminations (or tearing/crack) in base material are confirmed.
The laminations have to be considered a Crack and rejectable per 4.9.4.1(a) and the weld engineer’s requirement, correct?
Dale,
Leave it to me to be the dude that disagrees with the engineer.
Breaking my first "cardinal rule" of weld inspection (CR-1: Never evaluate a weld from a photo), the anomalies you've noted are not in the weld. Nor are they (with the exception of one) in the H.A.Z. (heat affected zone). Nor do they run in a direction which would suggest a welding related problem.
If you have concluded that these are laminations (Dye-Pen [PT] would confirm) they would not be included in 4.9.4.1
These laminations should be evaluated per the material specification of the base material (ASTM A36). That should be the criteria used to determine acceptance.
On the other hand, the beauty of being the "Engineer" is that your word is final. So if you're asking me, I say this weld is acceptable and the laminations should be evaluated per ASTM A36, but you go with whatever the Engineer determines.
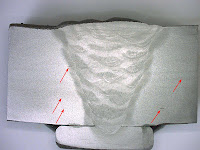
The laminations have to be considered a Crack and rejectable per 4.9.4.1(a) and the weld engineer’s requirement, correct?
Dale,
Leave it to me to be the dude that disagrees with the engineer.
Breaking my first "cardinal rule" of weld inspection (CR-1: Never evaluate a weld from a photo), the anomalies you've noted are not in the weld. Nor are they (with the exception of one) in the H.A.Z. (heat affected zone). Nor do they run in a direction which would suggest a welding related problem.
If you have concluded that these are laminations (Dye-Pen [PT] would confirm) they would not be included in 4.9.4.1
These laminations should be evaluated per the material specification of the base material (ASTM A36). That should be the criteria used to determine acceptance.
On the other hand, the beauty of being the "Engineer" is that your word is final. So if you're asking me, I say this weld is acceptable and the laminations should be evaluated per ASTM A36, but you go with whatever the Engineer determines.